Injection
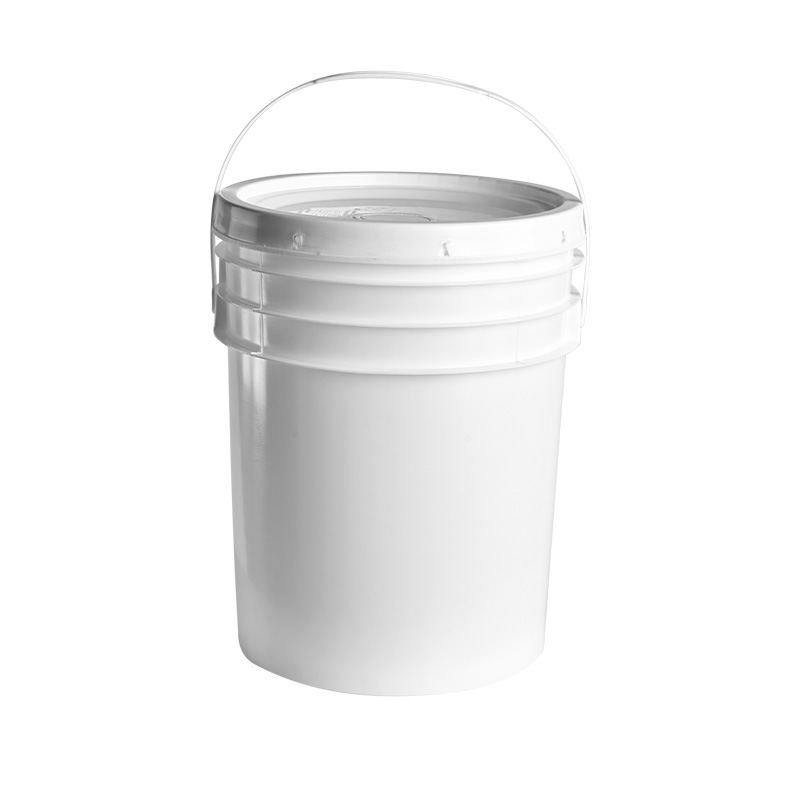
Buckets
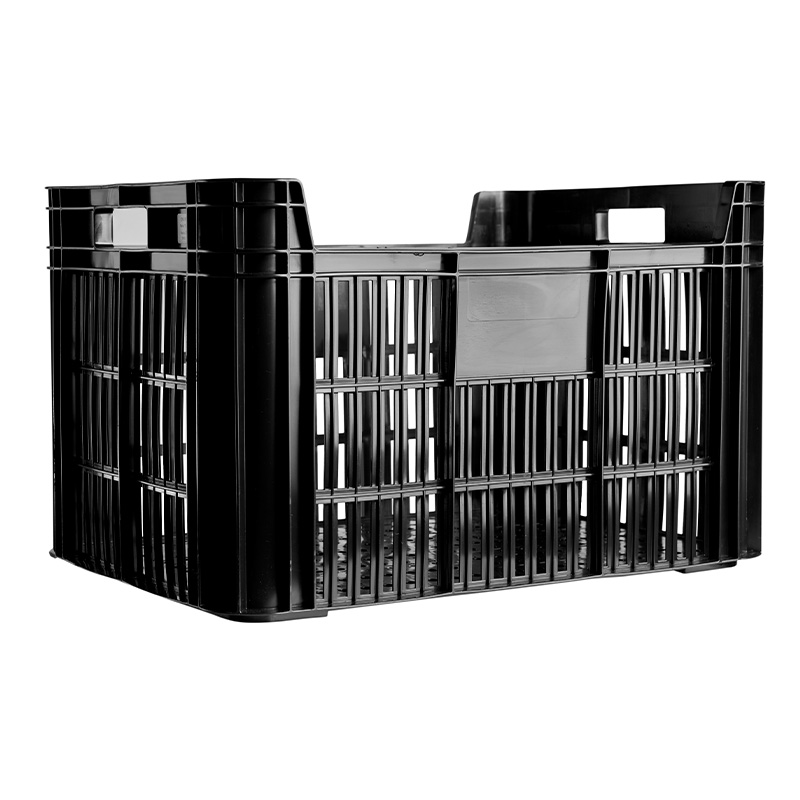
Containers
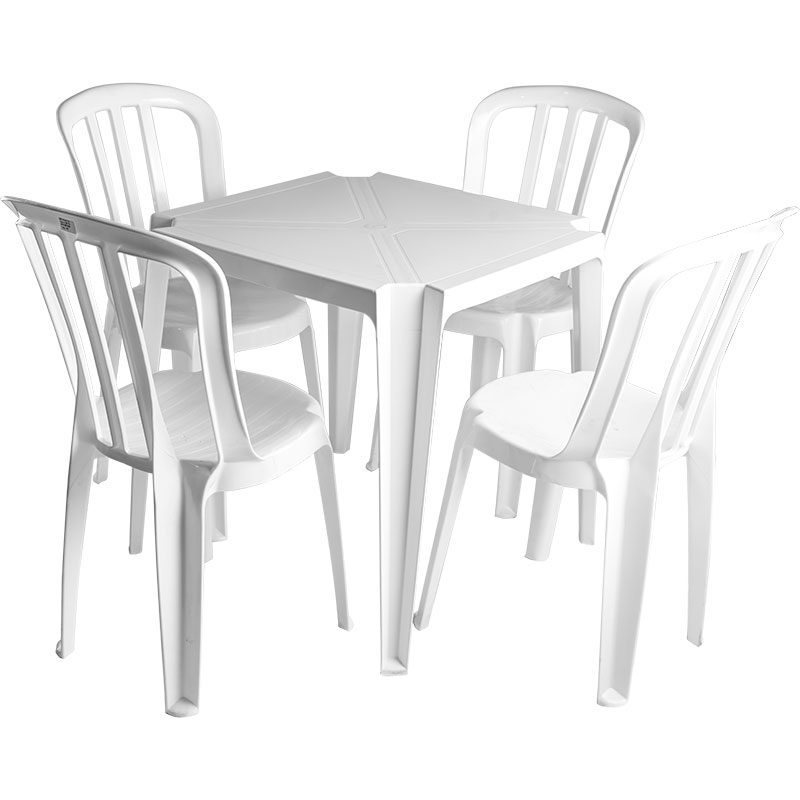
Furniture
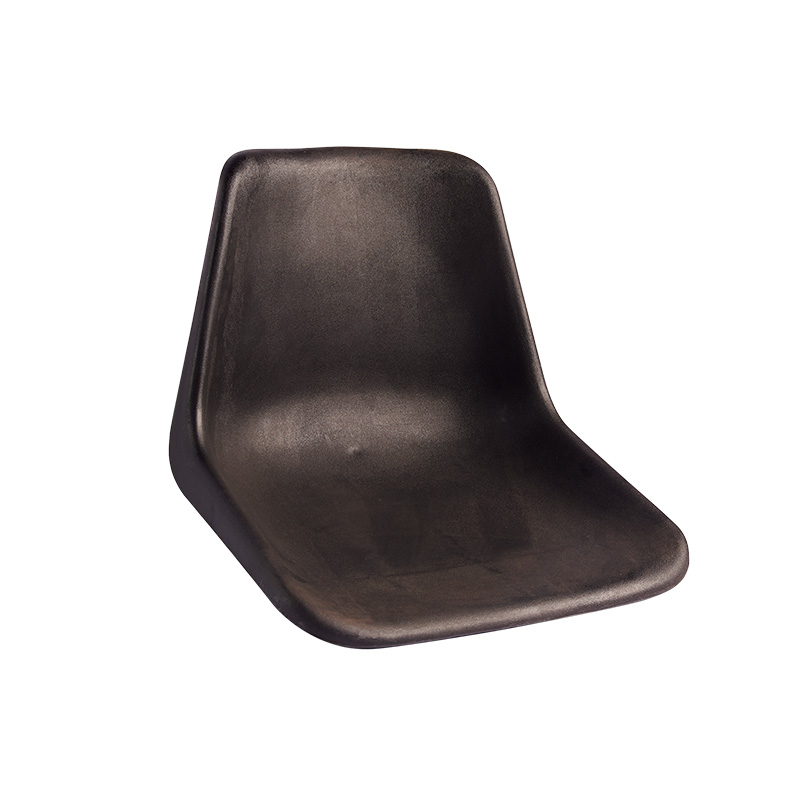
Other
Injection Process
PROCESS
Injection molding is one of the most famous plastic processing technologies, as it represents a relatively simple way to manufacture components with highly complex geometric shapes. This requires an injection machine that includes a mold. In the latter, a cavity is made whose shape and size are identical to those of the part to be obtained. The cavity is filled with molten plastic, which solidifies, maintaining the molded shape.
INJECTION UNIT
The main function of the injection unit is to melt, mix and inject the polymer. To achieve this, screws with different characteristics are used depending on the polymer to be melted. The study of the polymer melting process in the injection unit must consider three thermodynamic conditions:
The polymer processing temperature.
The heat capacity of the polymer Cp [cal/g °C].
The latent heat of fusion, if the polymer is semicrystalline.
The melting process involves an increase in the heat of the polymer, which results from the increase in temperature and the friction between the barrel and the screw. Friction and shear stresses are essential for efficient melting, since polymers are not good conductors of heat.
An increase in temperature decreases the viscosity of the molten polymer; the same happens when increasing the cutting speed. Therefore, both parameters must be adjusted during the process.
There are also standard metals for each polymer in order to avoid corrosion or degradation. With a few exceptions, such as PVC, most plastics can be used in the same machines.
The injection unit is originally an extrusion machine with a single screw, the barrel having heaters and sensors to maintain a constant programmed temperature.
The depth between the channel and the screw decreases gradually (or drastically, in special applications) from the feeding zone to the metering zone. In this way, the pressure in the barrel gradually increases.
Mechanical stress, shear and compression add heat to the system and melt the polymer more efficiently than heat alone, which is the main reason why a screw is used and not an autoclave to obtain the melt.
A substantial difference with respect to the extrusion process is the existence of an extra part called the reserve chamber. This is where the molten polymer accumulates to be injected.
This chamber acts like a piston; the whole unit behaves like the plunger that pushes the material. Because of this, a part of the screw ends up being underutilized, which is why long barrels are recommended for efficient mixing processes.
In both injection and extrusion, the PvT (Pressure, Volume, Temperature) relationships must be taken into account, which help to understand how a polymer behaves when melting.
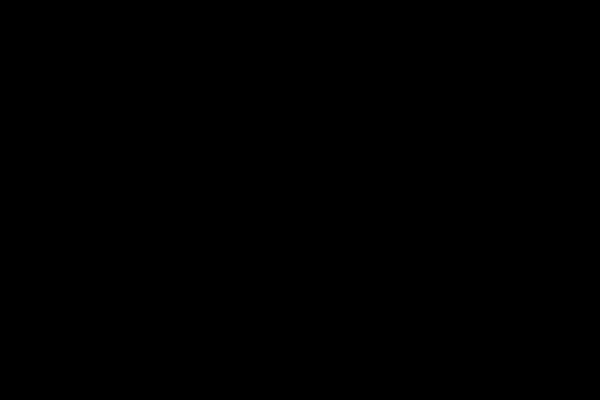